disadvantages of sheet metal forming process The disadvantages of sheet metal forming 1. High initial costs: Tooling and specialized equipment can be costly, making low-volume production runs less economical. Husky has different lines and therefore different gauge steel in each. Going from 20-22 gauge on the lowest end stuff to 18-19 on the midrange stuff (which is pretty expensive already), and then 16 gauge on the pro level stuff. I can't say for sure what category the one in the picture falls under.
0 · what is sheet metal forming
1 · types of metal forming process
2 · steel sheet metal forming
3 · sheet metal forming methods
4 · sheet metal forming examples
5 · how does sheet metal form
6 · disadvantages of sheet metal forming
7 · disadvantages of metal forming
Standard cabinets are built with premium quality steel and reinforced doors for long-term performance at an attractive price. Polished chrome handle uses three-point keyed locking to lock both doors. Punched lances in back facilitate ventilation. Shelves adjust in .
Sheet metal forming’s disadvantages aren’t enough to dissuade countless industries from avidly using it—its pros far outweigh the cons. In aerospace, sheet metal forming is used often for fuselages and the structural . Sheet metal enclosure manufacturing involves many different sheet metal forming processes such as roll forming, stamping, peen forming and .
The disadvantages of sheet metal forming 1. High initial costs: Tooling and specialized equipment can be costly, making low-volume production runs less economical. Metal forming is a process of manufacturing components of desired shapes by deforming the material plastically, by the application of compressive force, bending or shear . Sheet metal forming primarily applies tensile or shear forces and deals with sheets, plates, and strips. Sheet metal operations, such as bending, drawing, shearing, blanking, and punching, are commonly carried out using . Disadvantages of Metal Forming High Initial Costs : The tooling and setup required for many metal forming processes, such as stamping and extrusion, can be costly. These .
What Are the Advantages & Disadvantages of Sheet Metal Forming? Sheet metal forming has both advantages and disadvantages. The advantages include high production efficiency, cost .
There is no blanket rule in deciding whether or not a particular sheet metal stamping design is perfect or there are certain disadvantages to it. There are several processes involved such as the stretch forming, roll forming, stamping, . Coining has several advantages and disadvantages. It can produce sharp, crisp corners; well-defined features; and a brilliant surface finish. Because coining uses compression to form the part, tension failure is unlikely. .
Sheet metal forming’s disadvantages aren’t enough to dissuade countless industries from avidly using it—its pros far outweigh the cons. In aerospace, sheet metal forming is used often for fuselages and the structural components in aircraft and spacecraft.
Sheet metal enclosure manufacturing involves many different sheet metal forming processes such as roll forming, stamping, peen forming and more. This list compares the good and bad of each process so you can determine the proper one for your own unique requirement.
7. Sheet Metal Forming: It is a process where a sheet of metal is heated and then formed into its desired shape by using a tool or die. This process is often used to create display cases, brackets, and other similar items. Bending is a process where a metal rod or wire is heated so that it becomes soft enough to bend without breaking. The disadvantages of sheet metal forming 1. High initial costs: Tooling and specialized equipment can be costly, making low-volume production runs less economical.
Metal forming is a process of manufacturing components of desired shapes by deforming the material plastically, by the application of compressive force, bending or shear force, tensile force, or combinations of these all forces together, without adding or removing material. Sheet metal forming primarily applies tensile or shear forces and deals with sheets, plates, and strips. Sheet metal operations, such as bending, drawing, shearing, blanking, and punching, are commonly carried out using hydraulic or pneumatic presses. Die and punch sets are used in these sheet metal operations.
Disadvantages of Metal Forming High Initial Costs : The tooling and setup required for many metal forming processes, such as stamping and extrusion, can be costly. These initial expenses can be prohibitive for small-scale productions or companies without the necessary capital investment.What Are the Advantages & Disadvantages of Sheet Metal Forming? Sheet metal forming has both advantages and disadvantages. The advantages include high production efficiency, cost-effectiveness, versatility, and more. However, there are also challenges such as limited material thickness and high tooling costs. Advantages of Forming Sheet Metal
There is no blanket rule in deciding whether or not a particular sheet metal stamping design is perfect or there are certain disadvantages to it. There are several processes involved such as the stretch forming, roll forming, stamping, drawing, and so on. Coining has several advantages and disadvantages. It can produce sharp, crisp corners; well-defined features; and a brilliant surface finish. Because coining uses compression to form the part, tension failure is unlikely. One disadvantage is . Sheet metal forming’s disadvantages aren’t enough to dissuade countless industries from avidly using it—its pros far outweigh the cons. In aerospace, sheet metal forming is used often for fuselages and the structural components in aircraft and spacecraft.
Sheet metal enclosure manufacturing involves many different sheet metal forming processes such as roll forming, stamping, peen forming and more. This list compares the good and bad of each process so you can determine the proper one for your own unique requirement.
7. Sheet Metal Forming: It is a process where a sheet of metal is heated and then formed into its desired shape by using a tool or die. This process is often used to create display cases, brackets, and other similar items. Bending is a process where a metal rod or wire is heated so that it becomes soft enough to bend without breaking. The disadvantages of sheet metal forming 1. High initial costs: Tooling and specialized equipment can be costly, making low-volume production runs less economical.
Metal forming is a process of manufacturing components of desired shapes by deforming the material plastically, by the application of compressive force, bending or shear force, tensile force, or combinations of these all forces together, without adding or removing material. Sheet metal forming primarily applies tensile or shear forces and deals with sheets, plates, and strips. Sheet metal operations, such as bending, drawing, shearing, blanking, and punching, are commonly carried out using hydraulic or pneumatic presses. Die and punch sets are used in these sheet metal operations.
Disadvantages of Metal Forming High Initial Costs : The tooling and setup required for many metal forming processes, such as stamping and extrusion, can be costly. These initial expenses can be prohibitive for small-scale productions or companies without the necessary capital investment.What Are the Advantages & Disadvantages of Sheet Metal Forming? Sheet metal forming has both advantages and disadvantages. The advantages include high production efficiency, cost-effectiveness, versatility, and more. However, there are also challenges such as limited material thickness and high tooling costs. Advantages of Forming Sheet MetalThere is no blanket rule in deciding whether or not a particular sheet metal stamping design is perfect or there are certain disadvantages to it. There are several processes involved such as the stretch forming, roll forming, stamping, drawing, and so on.
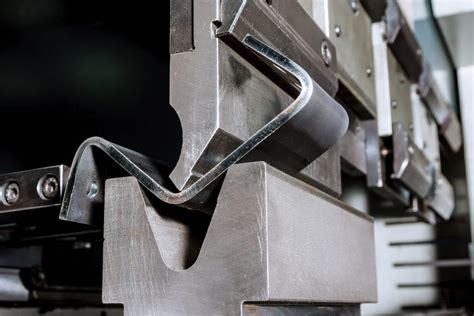
what is sheet metal forming
types of metal forming process
CNC machining is a subtractive manufacturing process that involves removing part of a workpiece using instructions from a CAD model to make a product.
disadvantages of sheet metal forming process|steel sheet metal forming